If you’re here checking out my site after my presentation, you can check out all the slides from my presentation above. If you’d like more information about the individual things in the slides, I posted an update for most of them over on Hackaday. If you’ve still got some questions, feel free to leave a comment below, hit me up on twitter, email me directly.
Category Archives: Things I Learned
Organizing
Everyone utilizes their own method of organization, notetaking, and motivation. Some use “Getting Things Done,” others go with “Inbox Zero,” or the “43 folders,” there’s Jerry Seinfeld’s “Don’t Break the Chain,” and a new one called the “Bullet Journal.”
I’ve tried some of these methods, combinations of these methods, and here’s what I’ve come up with for my own life.
- E-Mail
- Reply quickly.
- As Tony Soprano once said, “more important than the particular decision is that it happen in a timely fashion.” My number one rule of email management is simply this – reply immediately to anything that deserves a reply. Any timely response, even a non-optimal one, is better than a polished late response.
- If you can’t get a quick response out because some action is required…
- Act or Delegate, even to yourself. If there’s something to be done, do it already. From now on, you live in a world of “to done’s” not “to do’s.” If you can’t do it, then figure out what needs to happen first and work on that. If someone else needs to do it, ask them to take care of it and let you know when they’re done. If you need to do something else, copy yourself on the email and ask yourself to do it. Your own email will arrive in your inbox and you’ll need to…
- Start a draft. If the matter really requires more information than you have at your fingertips or isn’t urgent, start a draft.
- Turn drafts into emails. Every day turn drafts into emails and send them out. Since my job has become roughly 80-90% email, this is how I manage it all.
- Ignore unimportant emails. Most of your emails are unimportant. Ignore them, mark read, move on.
- Reply quickly.
- Web Surfing
- Tabs. Tabs are the enemy. They will rob you of your productivity. If you open a tab, read it, enjoy it, and close it or decide it is information you want to retain. If it is truly important and something you’ll need to refer to all the time, bookmark it. But, remember…
- Bookmarks. Bookmarks are the enemy. These are kept to an absolute minimum and only for sites you really visit all the time. Otherwise, that information you wanted to keep will be lost in difficult to search bookmarks forever.
- Everything else. If you find a web page, tweet, or some other information that you want to keep or reference in the future, share it or make a note.
- Sharing
- If you share information you help a friend and preserve the information in your sent folder, twitter stream, etc. Otherwise, make a note. The thing with notes is…
- Notes
- There are only two kinds of notes in the world. Information that is of temporary use and information that is of permanent use.
- Temporary notes. Write these on whatever you have lying around. Discard when done.
- Permanent notes. A permanent note really comes down to how you want to treat information. I like information either in an electronic searchable format or I want it written down so I can reflect on it or refer to it later. A permanent electronic note goes into Google Keep or an email to myself, in outine format, listing things in no particular order, with a few keywords in the subject line and body of the email near the link. When I need to find it again, I just search in Google Keep or for emails from me and specific keywords. A permanent written note goes in my…
- Notebook
- The problem with the Bullet Journal method is that it requires setup, discipline, and maintenance. If you screw those up, the notebook and all the lovely page numbers and organization systems become a burden, a hassle or, worse, useless.1
- There are so many great things about keeping a notebook. It’s a quick and easy way to record interesting and useful information. While my handwriting is horrible, but I’m pretty decent at drawing and sketching. A notebook for me is something where I can brainstorm, start drafting an idea I can return to later, or where I can record information for posterity. I tend to work out ideas on scraps of paper before recording that data in a more permanent format by committing it to my notebook. Sometimes this means copying information by hand or, my personal favorite, literally cutting and pasting information into the notebook. The worst thing is probably that it isn’t particularly searchable.
- Title and Date. Every entry in the notebook starts on a fresh page with the date at the top right corner and a helpful title at the top of the page. The date does more than provide you with context.
- Cross Referencing. The dates at the top of the page function as your page numbers. When you need to refer to a page in the past, rather than referencing a page number, just reference the date of the prior page. When you write a cross reference down to a prior page, note the future date on the prior page.
- DIY Flags. I placed several pieces of duct tape inside the front cover of the notebook. On top of that, I put several small 1/2″ x 1″ pieces of duct tape. These can be peeled off easily and folded over a page for a sturdy bookmark. More on this later.
- Well, this is my theory. I don’t actually know since I haven’t actually tried the Bullet Journal method… [↩]
How to Make Awesome Cardboard Paper Mache Anything
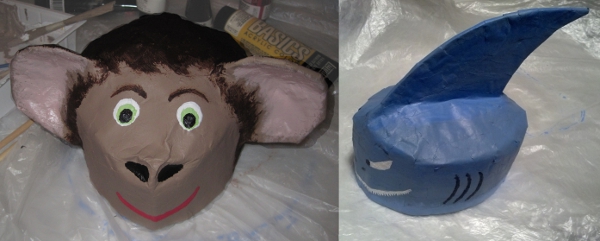
Awesome Paper Mache Hats
A few weeks ago a friend of mine had a “bad movie night” where he was showing the film1 “Sharknado.” Inspired by the theme for the party, I decided I had to wear a shark hat for the event. After making my hat, my daughter requested a monkey hat. This was not a request I could refuse.
I took pictures of the process to show you how you can make your own. I haven’t ever tried to make paper mache hats before, so this was not only a lot of fun – but a great learning experience. While I own the really great paper mache monster books by Dan Reeder, I only used them for inspiration and tried out a few new things on my own.
Even though I used this process to make hats, the directions here could easily be adapted to making anything out of paper mache.
1. Step 1: Gather Materials and Tools

All the things you need to make your own awesome paper mache anything
Here’s what you need to get started:
- Cardboard Boxes. Cardboard forms the “skeleton” of the structure. It’s cheap, ubiquitous, sturdy, and easy to cut and form.
- Masking Tape. Once the cardboard has been cut, liberal use of masking tape will keep your creation together until it can be covered with paper mache.
- Scissors and Utility Knife. Scissors can be very helpful in cutting cardboard or paper. While scissors can be helpful, and appropriate for kids, I find a utility knife gets the job done faster.
- Measuring Tape. If you’re not making a hat (or other apparel or armor) you won’t need this. But it is helpful when making measurements. ((In a pinch, you could just use a piece of yarn or string to mark lengths, and then put the yarn on the cardboard for reference.))
- Plastic Wrap. Whether you’re working with gluey paper or paint, the process is messy. I would recommend covering the work surface with plastic wrap. I happened to have a really large plastic bag, which I taped directly to the table.
- Glue. I just used a big bottle of Elmer’s white glue from the hardware store, but I’m pretty sure wood glue would have worked as well, if not better. It’s also more versatile and sturdy.
- Plastic Tray. The next time you get take-out or have a plastic liner from inside some packaging, save it. It makes a great wide tray for mixing water and glue or when your project is dry, it is also great for mixing paints.
- Paper Grocery Bags. The “twist” with this process is that I used torn up grocery bags, rather than the traditional newspaper. It turned out this was a really good idea for a number of reasons. Paper bags are a cheap and plentiful material. When thoroughly wet strips of paper bags are easy to place, mold and shape. However, the most important features of paper bags is that they hold glue and water really well and then dry quickly into a sturdy hard shell. In fact, they form such a sturdy surface that I only had to do a single layer of paper mache around the entire hat. This means that you can quickly put down a single layer of paper bag strips all over your cardboard form, wait a few hours for it to dry, and then get to work finishing the project.
- Paper or Newspaper. While grocery bags work really well to cover your cardboard form, they can leave some small gaps where they overlap. When I found gaps in the project, I simply used a few thin strips of the newsprint style paper to cover the holes and smooth out spots on the rough paper bag layer.
- Cup of Water and Paintbrushes. An old mug is best and pile of cheap dollar store brushes is probably fine.
- Paints. I prefer acrylic paints. They are cheap, can be diluted with water, easy to mix, they stay wet long enough for you to blend, but not so long that you have to wait days for it to dry. They also clean up well with water.
2. Step 2: Create Cardboard Form

Process for creating awesome hat
The process I used to create the cardboard forms for the hats was pretty quick and easy. I measured the circumference of my daughter’s head and then the distance from her ears to the top of her head. Using these measurements, I cut out a strip of cardboard as tall as the distance from her ears to the top of her head and as wide as the circumference of her head – with a little extra to allow for overlap.
In the pictures above you can see the strip of cardboard cut out and then taped into a cylinder with the masking tape.
Cut strips into the cardboard cylinder, fold them down, and add enough masking tape to mold it into a hat-shape.
3. Step 3: Add Embellishments
A paper mache hat is way more interesting with some kind of embellishment, like ears, shark fins, wings, or whatever else. Here I cut ear shapes out of cardboard, curved them slightly, taped them to hold the curve, and then taped them to the hat. When I made the shark hat, I cut a long slit into the hat through the tape and inserted the shark fin through the underside of the hat. Don’t be afraid to use a lot of tape.
4. Step 4: Prepare the Work Surface, Paper Strips, and Glue Mixture
Cover the work surface with plastic sheeting. I used a big plastic bag from a helium balloon order from my daughter’s birthday. However, a big garbage bag or plastic wrap would also work well. Paper bags from the grocery store work really well – but there are too thick in places. Tear off the handles and pull the paper bag apart at the seams. You’ll probably need to discard some of the sections where the the paper bag is too thick to use.
Add some glue (I used about a tablespoon) and warm water (about a half cup or so) to the plastic pan. It should look like milk or heavy cream once you’ve mixed it up.
Completely soak the strips of paper bag in the glue mixture. They should be completely soaked all the way through until they’re nearly translucent. Unlike paper mache with thin pieces of newspaper, you won’t need to put layers and layers of paper on the form – just one layer where the pieces overlap a little should work fine. The excess glue from the strips of paper will soak into the cardboard and help make the entire structure sturdy.
5. Step 5: Set Model to Dry, Patch Holes with Paper
Since the cardboard helps soak up the water, the entire structure should dry relatively quickly. I put the shark hat outside in the sun for a few hours and it was ready for painting. Once the hat is dry (or dry enough), you’ll probably notice some holes and gaps from the paper bag strips. Tear up some newsprint paper, soak those in the gluey mixture, and cover and smooth out any defects. Once these pieces dry, the project will be ready to paint!
6. Step 6: Paint to Suit
The great thing about acrylic paints is that they are so easy to work with. They dry really quickly, so you can paint one side of the model, work on the other side, and then come back to the first side to add details. In any case, just paint the project to suit and you’re done!
Each hat went together really quickly. I put the cardboard form together in about 15 minutes, covered it with the gluey paper bag strips over maybe 30 minutes, let it dry for several hours, and then paint it over the course of maybe an hour.
If you make your own paper mache hat (or other sculpture), let me know in the comments!
- And I use the word “film” loosely here [↩]
Maker MBA
I’ve been investigating the possibility of trying to make a business out of making.1 This got me thinking about the best series and the best single post about making money out of making. I got a lot out of these posts and I hope you will too:
- Ten Rules for Maker Businesses – Rule #1 Make a Profit. Chris Anderson, author, entrepreneur, and named as one of the 100 most influential people in the world by Time, has probably written the best “Ten Rules” list for a maker who is considering selling stuff. I’d rather have this list in my back pocket than an MBA any day.2 If you ever think about selling anything you’ve made, you should read every one of these posts:
- Make a profit
- It takes a lot of cash to stay in stock
- Buy smart
- Basic business rules still apply
- You get no leeway for being a maker
- Be as open as you can
- Create a community to support and enhance your products
- Design for manufacturability
- Marketing is your job
- Your second most important relationship is with your package carrier
- How the Innovation Economy is Turning Makers Into Manufacturers by Chris Anderson. This is another Chris Anderson article – this time he’s writing with the benefit of the experience of having moved from a magazine editor-in-chief fiddling with one of the first 3D printer kits to cofounding 3D Robotics and becoming an entrepreneur. Since his open source hardware drone company just raised $30 million in venture capital, he’s probably the kinda guy you wanna listen to.
- The Slowest $380 I’ll Ever Make. This is the tale of a man with a dream – a dream of making and selling electronic LED QR Code clocks. Michael Ciuffo covers the money he made, lost, and made in painfully excruciating detail – with more than a little levity. This is a cautionary tale for anyone looking to sell something awesome in their spare time – and some of the dangers hidden in success.
- How To Build A Hardware Startup – A complete guide from idea to market fit by Marc Barros. This book by Marc Barros is published online at Adafruit along with a number of their posts under the heading of “maker business.” I’ve only breezed through it, but it seems to contain a lot of focused detailed information and advice.
- Photo courtesy of Poster Boy [↩]
- Besides, no one makes pocket sized business school graduates, amirte? [↩]
SpiderBot – once more into the breach!
So, I’m about to begin a completely new design on my little spider bot using what I’ve learned from the last try.
Failure is fun!
It’s alive!
I’ve got my Thing-O-Matic operational. There were some initial hiccups, but it seems to be working. However, I definitely need to calibrate Skeinforge and the “end.txt” cool down settings for this machine. More on those details over at the MakerBot blog. My initial print, a mini mug1 , turned out reasonably well – but is a little too sparse for actual toasting.
- Natch [↩]
What am I supposed to do with all of these obsolete parts?
I love love love the idea of repurposing a MK4 plastruder into a plastic welding gun. Although, you could probably build a reasonable welding gun out of scrap parts even if you had only a MK4 – since it really only requires the PTFE barrier, barrel, nozzle, and some nichrome.
MakerBot woes
Building my MakerBot and getting it printing reliably was challenging, but totally doable by a technical novice such as myself. I have lots of people on the MakerBot Operators group to thank for their patience and help in getting my MakerBot online. 1 Looking back, I spent about a month building and then calibrating my ‘bot. 2
It’s easy for me to forget that first month of occasional frustrations and triumphant victories, now that I’ve been printing successfully for more than eight months. It actually makes me a little sad when I read people writing about their own frustrations and how they’re ready to throw in the towel. The most recent example was noobcake getting frustrated with her ‘bot and getting ready to sell it off in parts. Thankfully, Spacexula swooped in to help her out.
This brings me to We Alone On Earth‘s recent post. WAOE are a group of introspective, philosophically and technologically minded twenty-somethings. To give you you an idea of their frustration with their ‘bot, the post was entitled, “MakerBot: not very much fun at the moment (caveat emptor)” Yikes. 3 I realize that WAOE has revised their original post several times since the original publishing date – but they have a lot of legitimate concerns.
WAOE list off seven problems with the MakerBot. I’m not going to refute these points – but rather offer another perspective on them. After several updates, WAOE offer additional comments, I’ll include them here in “[]”.
- The PTFE is prone to melting. [WAOE expects the new MK5 Plastruder will resolve this issue]. I have never heard of a PTFE barrier melting. I’ve heard of them deforming from a blockage and had one develop a clog which I had to remove. Several people have purchased MakerGear PEEK replacements – but these are far from necessary. I clogged my first barrier once, cleared it, clogged it again, and am now using a slice of it as an insulating washer.
- Inexplicable printing behavior due to noise. [WAOE fixed this issue by twisting wires and installing a resistor]. I’ve never had this problem, but I know others have. Like WAOE, I’ve heard of people fixing these issues by twisting wires, using resistors, or ferrite beads. Perhaps my workstation has less electronic noise, but I haven’t had to do any of these things. Then again, perhaps my prints suffer from a certain degree of noise?
- Printing large objects is hard without a heated build plate. [WAOE notes this isn’t an issue if you’re good at soldering]. Totally true for ABS, but not PLA.4 However, this is really a problem with the print media – not with the printer, right? ABS will warp as it cools, unfortunate but true. I’ve had less warping problems in warm weather or during with a second print – basically when the build platform is already warmed up. Zaggo’s printruder is one of the largest things I’ve printed. Interestingly, his design takes into account that certain parts are expected to warp. 5 Or check out Clothbot’s train track – it was designed with a lattice/correlated bottom to prevent warp problems. Plastic warps – but with careful and thoughtful designing, this shouldn’t be a limitation.
- The heated build platform is difficult to build and requires a relay kit. [WAOE notes this isn’t an issue if you’re good at soldering]. I can’t dispute either point. I just got both and haven’t had a chance to assemble them yet. I’m assuming the heated build platform, which requires SMT soldering, will be challenging. Frankly, fear of SMT soldering was the big reason why I didn’t jump into buying a MakerBot sooner. 6 The MakerBot HBP is just one option for a heated platform – there’s several others out there. Don’t like SMT soldering? Try out Rick’s platform over at MakerGear. More into DIY? Well, use the plans posted for any of several other variations. As for the relay kit – it’s not a requirement – but it will prevent MOFSETs from burning out on your extruder motherboard. 7
- Calibrating Skeinforge is hard. [WAOE notes this is still an issue]. I like to use the word, “challenging.” A better way to look at MakerBot calibration is that you get out of it what you put into it. I have my MakerBot tuned to the point that I get reasonably good looking durable parts. Sure, I could spend more time and get even better looking parts. However, once I got it printing reliably I was much more interested in printing new things than refining the printing process. I’ll get around to improving the print quality even more – but I’m having too much fun right now.
- The Plastruder MK4 feed system is unreliable. [WAOE expects the new MK5 Plastruder will resolve this issue]. Getting the tension on the MK4 idler wheel is just one of those aspects of my MakerBot I had to experiment with and get just right. I’ve been printing reliably for eight months using the same idler wheel and gear. With proper maintenance, flossing the extruder, and clearing chips out of the extruder the current setup is serving me well.
- The threaded rods are of poor quality. [WAOE are getting new threaded rods, which should fix their problem.]. Of my four threaded rods, one is definitely warped and two have very minor warps. By experimenting, rotating them just so, and printing a few wobble arrestors I’ve eliminated most of these issues. You can definitely get more expensive and straighter threaded rods and improve your build quality.
A MakerBot Cupcake CNC kit is not for everyone – but the kit can be build and operated by anyone who is willing to invest the time to do so. It is a cheap, hackable machine that is literally going to be just as useful as you make it. Want less warpage, higher resolution, more reliable extrusion? You can buy an upgrade, build one from their plans, or design your own solution. 8 Want a CNC mill, CNC pencil, or CNC music box? Design the very first one! Then again, you don’t have to do any of these things.
A MakerBot kit is just a platform for your creativity. It’s just that big. 9
As for you, WAOE, if you want some help – drop me a line!
- If I had an acceptance speech, I’d go on and on while the music played. [↩]
- My first successful print was on 12/31/2009. [↩]
- Don’t get me wrong – I love my MakerBot, but I readily acknowledge its limitations. [↩]
- From what I heard. :) [↩]
- It was designed before availability or widespread use of heated build platforms. [↩]
- Well, that and a little thing called “money.” [↩]
- Did I get that part right? [↩]
- I haven’t installed a single non-printed upgrade. [↩]
- Or that small. :) [↩]
MakerBlock’s MakerBot setup
I’ve posted about other people’s MakerBot work space set ups,1 but not much about my own yet.
Right now there’s a bunch of junk2 in the way so no pictures of the setup for now. My MakerBot – “Bender,” a laptop3 , and a large long cardboard box with a wooden dowel running the length with badly cut cardboard spools holding what was once a 5 pound coil of black ABS4 , a very nearly 5 pound coil of clear PLA5 , and a full pound of white ABS I’ve never used. 678
All of this resides in our living room on an enormous former-library card catalog. For those of you youngsters out there, a library card catalog is the kind of thing you see in the background scenes of Warehouse 13. Imagine a huge chest about four feet tall that has lots of small, deep, drawers. It is what libraries used to use to store information about their collections – an analog database. Frankly, I didn’t realize the one I bought was quite so large. 9 It’s literally big enough for about six identical MakerBot/laptop/plastic coil setups to the one I have. 10 The drawers beneath the area where my Makerbot resides are devoted to tools and spare parts. Right now the surface is covered in a number of unfinished projects and some totally finished projects.
Library card catalogs are super handy and useful ways to incorporate storage and a raised level surface for working. The only problem is that these things are absolutely enormous and way way heavier than they look.
- Mattpr’s MakerBot cart , Tony Buser’s “Tea” #481 [↩]
- FYI, junk = stuff waiting to be made into other, more useful or more amusing stuff. [↩]
- Named Bleys, if you must know. [↩]
- I would guess I’ve used about a pound over the last 8 months. 5 pounds is a LOT of plastic. Dear faithful ABS, oh how I love thee… [↩]
- Polly!!!!!!!!! [↩]
- Though, I have very specific and immediate plans for it. [↩]
- More on this later if you remind me. I have a tendency to get lost in nested footnotes and parenthetical references. [↩]
- Seriously, just imagine what my PHP code looks like. Yikes! [↩]
- Or far away. Or would become so expensive. That’s a story unto itself. [↩]
- I best get printing more MakerBots, no? Hmm… I might have to print more laptops too… [↩]
Sometimes a good deal isn’t
Several months ago I made an impulse buy at the local hardware store. I picked up a utility knife that came with 6 blades for $1. It was a good deal, if even for just the razors, and I couldn’t find my usual $3 knife.
Here they are, side by side. My trusty Stanley utility knife on top. This knife has a good heft, stores a few extra blades in its handle, and is slightly wider, making for a more comfortable grip. The two sides also interlock as well as screw into one another. Clicking the blade out another notch requires a small amount of force – just enough so you’ll never do it by accident – and so that it will stay in each notch as long as you don’t intentionally depress the button.
On the bottom is my no-name brand knife. It’s lighter, slightly thinner, rattles with the extra blades inside, and the button to extend/retract the blade has a little bit of wobble and play to it. Also, there’s no interlocking between the two halves.
I discovered that the seams between the two halves of the cheapie utility knife left a lot to be desired. While using the knife I felt a sharp poke in my palm. Turns out that some of the spare razor blades were poking through the incomplete seam.
So, if you’re headed to the hardware store, invest the extra $2 in the better knife. :)