Quick lead in: I am trying to build a cephalopod robot shoulder friend.
I was disappointed that I only learned of Glow Ascii‘s owl robot companion, Archimedes, after Maker Faire Bay Area 2018. Over the year, leading up to Maker Faire Bay Area 2019, I followed Odd_Jayy‘s spider/bowler Anansi robot companion with similar rapt interest.
Still high off Maker Faire 2019 , I was also excited by the prospect of #CephalopodWeek on NPR’s ScienceFriday. Between cuttlefish, squid, and various octopuses (especially the “Opisthoteuthis Adorabilis“), there are a LOT of awesome little friends to consider making.
While trying to avoid work, I posted a sketches to Twitter.
Hello Octo!
Early sketches
Designing tentacle segments
Opisthoteuthis Adorabilis Automata
Last week I started designing a few parts, drawing from some experience designing printable prosthetics for the E-nable project a few years ago. I was trying to build it out of what I had on hand, which did not include elastic cord. I thought a zip tie might provide enough “spring” and “give” to work.
Step 1: Measure and model a zip tie
This might work!
What would the curled bit at the end of a tentacle look like?
This might look like a tentacle?
What am I doing?!
Ugh. What have I done?
It’s a piece of crap! It doesn’t work!
I admit, this was a total mess. I suppose it is only fitting I use this meme featuring Dr. Zoidberg.
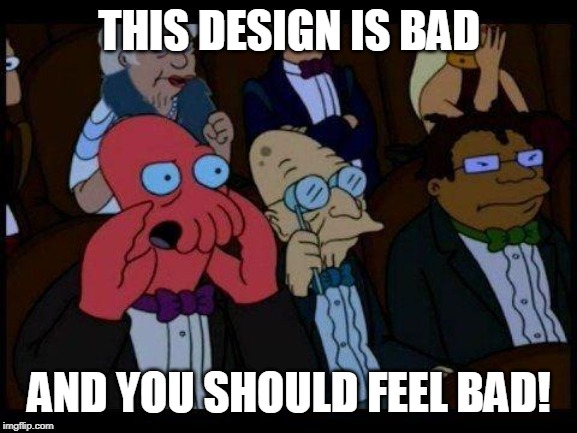
Thanks Dr. Z
Thanks to some kind encouragement from Odd_Jayy, I kept moving forward. Rather than focusing on the end of the tentacle, I got to work on the basics of the mechanics – channels for the elastic cord and fishing line, wedges cut into the faces so the tentacle could articulate.
Version 1 (because I’m disavowing the prior version)
Another view
The tabs on these parts were too thin and tended to break when I assembled them. However, the next version worked really well.
Now that’s more like it!
Underside view
Version 0, 1, 2, and 3
So I made more
And some more
These worked a lot better, so I started cranking out parts.
https://www.youtube.com/watch?v=QLUkgY5XDNg
https://www.youtube.com/watch?v=H–MmB1uzrA
The nice thing about these tentacles is that they look somewhat lifelike without actually requiring much in the way of electronics. As long as I can design a body/housing and put a servo inside, that one servo could possibly pull on 8 different sets of fishing line to articulate all the tentacles at the same time. And, since it’s just fishing line, there’s no special routing of brake cables necessary.
The tentacles are somewhat larger than I would like, so that means where they connect to the body needs to be similarly large. There’s definitely room for improving the tentacle segments. I’ve already designed two different “ends” for the tentacles, so they’re rounded instead of exposed connectors, fishing line, and elastic cord. Also, to make the curling tentacle look better, I should angle the the top and bottom of each segment. Another improvement would be to rotate the articulation angle for different segments to give the tentacle a more organic look when moving.
However, if I don’t get working on the body of the robot, it’s not going to ever get done. Given the size of the tentacles, I’d need to have them all on one side, lest the little robot take over my entire shoulder. Here are some “Cuttle-Bot” sketches along with a robot body design. If you look at the design, you’ll notice the connectors are rotated to different angles. This is so that the tentacles would each spring back together towards each other – and then splay outwards when articulated.
Cuttle-Bot sketches
Body and tentacle connectors in place
However, this last design takes FOREVER to render in OpenSCAD. This is at least partially due to design and code inefficiencies, but also due to the number of spherical parts, facets, and “hull” operations needed to make these parts work.
I think I may want to try shrinking the tentacles slightly so I can build a smaller-bodied robot. Either way, I have to get cracking on at least some kind of housing/body and mounting motors/electronics before I can keep moving forward.
Companion Robots: Building Robot Friends- Cephalopod Robot Friend, the story so far
- Cephalopod Robot Friend Progress
- CuttleBot Body and OpenSCAD Design Tips
- An Assembled CuttleBot Body
- Building the Monocle Top Hat Cat for #MicrobitVirtualConcert
- Companion Robots and Maker Faire Season!