After mentioning long render times on my machine, @raster suggested switching to the manifold 3D rendering backend. Depending on your OpenSCAD version, you might need to poke around to find how to enable this option. It’s absolutely worth your time and should really be enabled by default.
If you dig into this option a little, and you’re a 3D printing old timer, you might recognize the creator of this library as none other than Emmett Lalish!!! Emmett was an early 3D printing adopter, from back in the MakerBot Thing-O-Matic days, creator of the original heart gears, and just all around incredible engineer. 1 2
Emmett’s manifold library dropped the render time for one of my designs from 300 seconds to… under 8 seconds. I literally used to avoid hitting F5 on more complex designs or avoid cranking up the facets so I didn’t have to wait for long renders. A single comment from a friend, telling me about an option written by another friend, has completely and permanently changed how quickly I’m able to iterate and design objects forever.
Here’s how you can instantly save tons of time with your OpenSCAD designs:
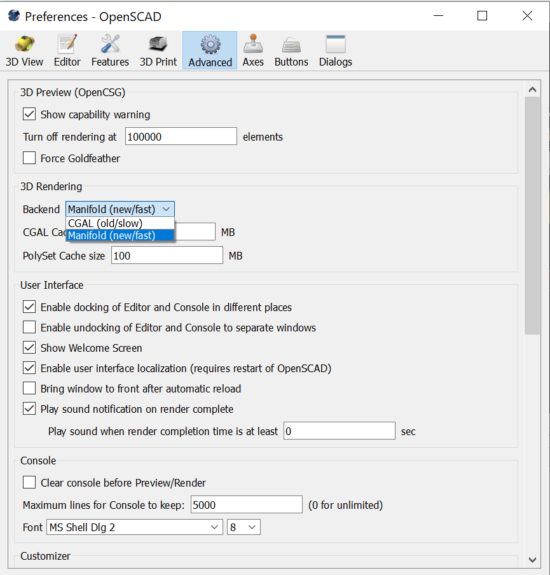
“Manifold (new/fast)”
- OpenSCAD 3D Printed Spring
- OpenSCADClub Week 2: Directional Pad
- OpenSCAD Render Times
- One Simple Trick Can Save You 30 Minutes…
- Emmett even wrote a guest post on this very blog about… 14 years ago?!?! Time flies, I guess? [↩]
- Special thanks to my honorary editor Andrew for catching a typo… [↩]