In the comments of a recent post Tony and I were discussing how we were each thinking about how to design and print an 11th Doctor sonic screwdriver. Let’s set aside the nature of the object in question for a moment and consider the constraints, problems, considerations, and potential design solutions.
There are a number of challenges facing one wishing to print this particular object. Although the discussion pertains to the design challenges and decisions in this project, I’m hopeful it will be helpful to myself or another when it comes to some other design. Thus, let us think only of the design challenges, problems, and potential solutions.
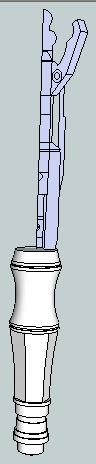
Sketch of Screwdriver
- This newest one is too large to be printed as one single piece.
- It has a number of overhangs.
- It has a number of moving pieces.
- It lights up.
- It is a comprised of a number of different colors.
- I don’t know the exact measurements.
Even if you want to print the non-extending, non-spring loaded, non-LED, non-swiveling bits there’s a fair number of considerations. Often my most successful way of solving a problem is to just get started and figure things out as I go.
In this case I got started by examining the pictures Tony and I had located. Quite separately we had both pulled the images out of the animated GIF. I created a new smaller image of the open and closed versions side by side, for comparison’s sake. Then, I reoriented both of them so they were vertical rather than on a slant. Then I resized the picture of the screwdriver in someone’s hand so that it was roughly the same scale as the other two images. This was placed next to the first two. I traced the images in Sketchup and spun the parts around and ended up with a reasonable facsimile of a portion of the screwdriver.
The problem with designing and printing in segments is figuring out how to assemble it.
- Snap-fit?
- Glue together?
- Bolt together?
- Friction fit?
- Do we design it so that it can be disassembled easily?
And, what about other considerations? If we want to install any electronics, lights, etc we probably want it to be easy to disassemble. Ideally, the entire assembly would be hollow in order to incorporate electronic parts. Besides, “if you can’t open it, you don’t own it,” right? That means no easy glue or snap fit solution. Bolting together means non-printable parts. I generally have a preference for 100% printable designs when I can manage. Here are some of the ideas I considered and dismissed:
- At first I was thinking of printing it in a series of tubes that fit over one another. This approach has several problems.
- I considered a screw thread approach. Basically a series of tubes which were screwed together. I wasn’t crazy about the idea of generating a number of helices, but would do so if a good design required. Although, I did like the idea of being able to just unscrew the entire thing when I wanted to take it apart. There’s also the very visceral act of assembly by taking all the bits off the platform, cleaning them, and screwing them together in about 15 seconds without any additional tools.
- A variation on the above. A system where the parts have a knob/groove connection similar to those very cool cylinder containers on Thingiverse. Twist, lock. It can be undone, and requires creating grooves instead of a helix, which is significantly easier.
- I considered a system where I create a long tube with a knob at one end. Then, create all the other parts so they can slide on. Affix something to the other end when done, glue/bolt, done.
- A variation on the above where all the parts are printed as tube, but press fit together. Designing them to the correct tolerances would be tough.
- Then I thought about printing it in vertical halves. Again, problems. Again, none are insurmountable, just problematic.
- Cosmetically, I’m not crazy about the nut/bolt holes which would be required to assemble two vertical halves.
- Alternatively, a snap-fit would be great – but a good one would not be easily un-snap-able.
- Press fit using circular tabs going into circular holes like every Happy Meal toy you’ve ever seen. There’s no real problem with this except that printing small nubs and circular holes is difficult. Then again, I could print larger holes/nubs. However, this means less room for a hollow interior.
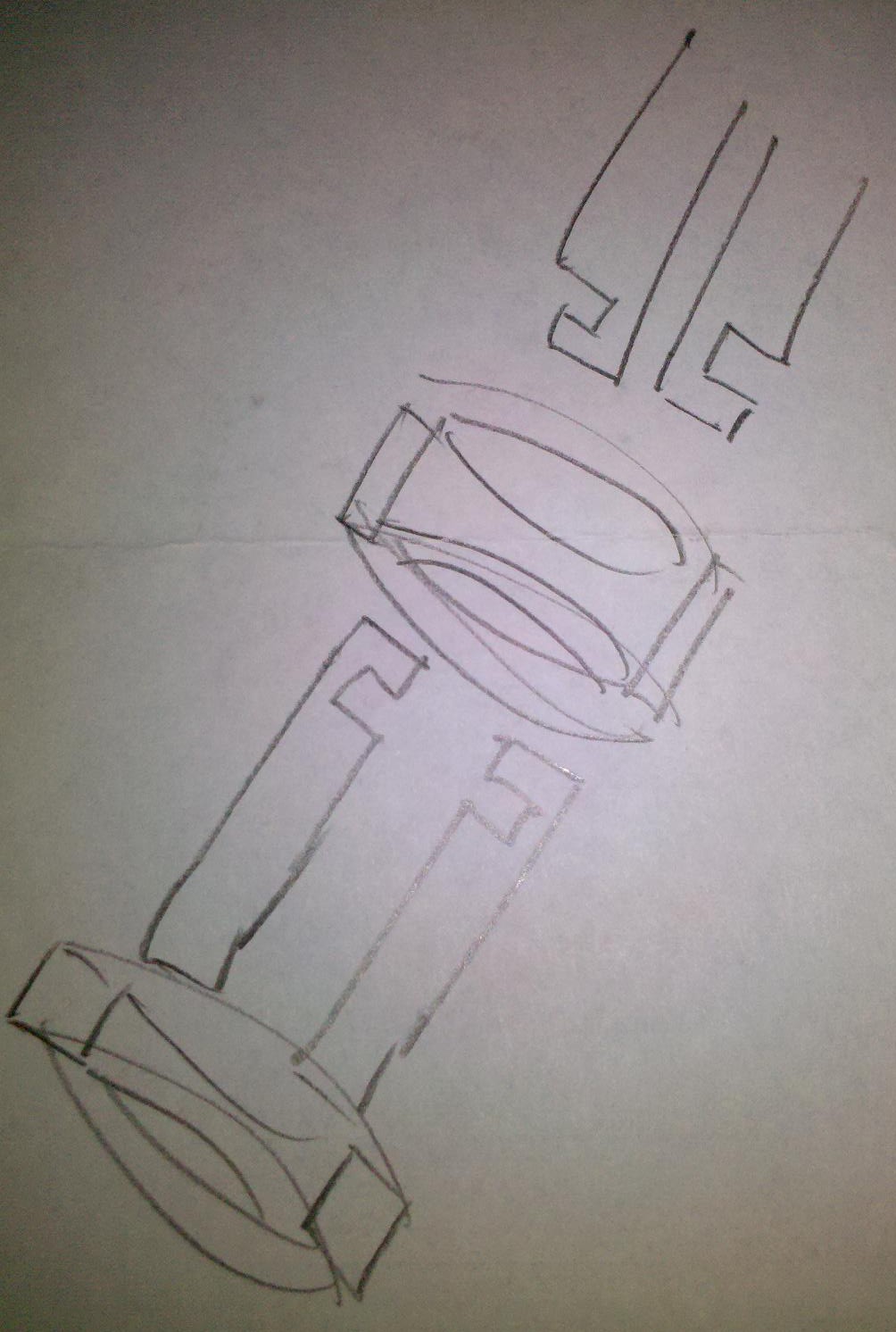
Napkin sketch
While sketching up the above in Sketchup I hit upon an idea. I could print the assembly in sections – but not necessarily similarly constructed sections. In this I was inspired by some of the design ideas I saw/recreated while creating a derivative 3x2x1 Rubik’s cube from TomZ’s 1x2x3 Rubik’s cube. If you look at the design of this style of Rubik’s cube (either of these will do) you’ll notice the two cubes at either end have little bits that stick out into half-cylinders which widen into half-disks. When you take two of these end cubes and set them together you end up with a full cylinder terminating in a full disk. These two are then captured in the two center cubes which have half-cylinder, half-disk grooves – which allow the two end pieces to rotate freely.
So, what if I printed large sections of the screwdriver as pieces that fit together vertically – but had a groove around the edge? You could leave the inside mostly hollow. Then, you could slide a ring or thin cylinder around it. If so, the ring would keep the two halves in place. The ring could be kept in place either by friction or a notch/groove system. The point is this design would:
- Allow the interior to be hollow
- Require only printed parts for assembly
- Not be overly complicated to design
- Be easily assembled and disassembled
Napkin sketch on right.
Amusingly, this only gets me 1/3 of the way. I still need to figure out how to design the bits that slide and the bits that swivel the claw like bits at the end. So, Tony, what you got?
Update: Cyrozap – sory fore mispellnig yoru mane.