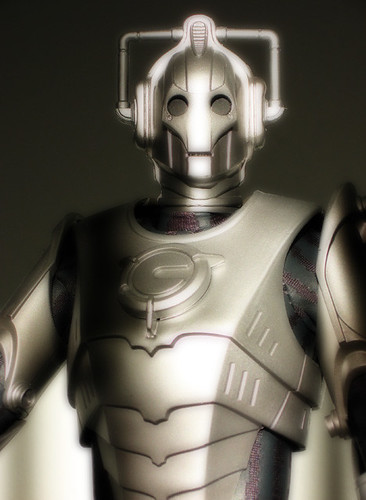
The plans for the Plastruder MK6 look downright wicked
MakerBot just released the photostream and wiki instructions for the Plastruder MK5. This looks like a total overhaul of their original designs.
It is based on Charles Pax’s Paxtruder which has such a small form factor that it is possible to squeeze two extruder heads into one Makerbot. The Paxtruder also uses a delrin plunger which is used to push the filament against the extruder pulley, rather than the previous idler wheel design. I like the delrin plunger idea since it would be a lot easier to adjust tension and remove/insert filament. The idler wheel held in by a large bolt and nut works… but is finicky and sometimes prone to fussiness.
Out are the big/small/weird and whimsical dinos in favor of lasercut acrylic “arches.” There may be a benefit to the arches over the dinos, but I’m not sure what it would be.
The entire heater element and extruder head has been redesigned as well. I don’t recall seeing any published designs which reference this new system. We’ve all seen power resistors in use in RepRap/MakerBot projects – but they’ve usually been relegated to heated build platform designs. Now a pair are being used as the full heating element in place of tempermental nichrome wire. The problem with the old nichrome wire wrapped around the barrel system is that if you need to rebuild the heater, you’ve got to toss out the old nichrome since the insulation is going to get peeled off as soon as you pull it off the barrel.
The new MK5 system uses a PTFE sleeve to feed the filament down into the heater. Interestingly, the PTFE sleeve is encased in a snug metal tube which should prevent any bulging problems.
My understanding of the instructions is that the MK5 is far less prone to failure than the previous MK4 model Plastruder. I’ll grant the Plastruder is easily the most challenging component of the Makerbot to get working.
The instructions also hint at Generation 4 electronics. Right now I’m rockin’ the Gen 3 which have served me quite well. I wonder what the Gen 4 has in store? One thing I have to really like about the electronics is that I know they’ll never really be obsolete. If I wanted to upgrade to Gen 4, I can always print off a Mini-Mendel or Mendel, and swap in the new electronics.
However, if this new system is as resilient as the instructions describe, I’m on board. I’m probably not going to have a good excuse to test out this new Plastruder design for a while since my Plastruder has been behaving itself since the last time I rebuilt my Plastruder and I just scored some spare MK4 parts.